Почему важно снижать потери при переналадке
В производстве время — это деньги. Каждый простой машины из-за замены оснастки, перенастройки параметров или подготовки нового сырья снижает общую эффективность оборудования. Эти паузы редко попадают в фокус руководителей, потому что они регулярны и кажутся нормой.
На большинстве производств переналадка занимает от 10% до 40% общего времени работы оборудования, SMED позволяет сократить время переналадки в 2–5 раз.
Пример: На упаковочном производстве замена рулона, перенастройка формата и протяжки занимала 45 минут. При 6 переналадках в смену — это 4,5 часа, или более половины смены. Производство успевало выпустить всего 50–60% от возможного объёма.
Потери при переналадке — это:
- ↓ производительность (меньше выпуска за смену),
- ↑ себестоимость (больше часов и амортизации на единицу продукции),
- ↑ напряжение команды (всё надо успеть за меньшее время),
- ↑ риск брака (при спешке, при ошибках наладки).
Методика SMED (Single-Minute Exchange of Dies) позволяет системно сократить время переналадки в 2–5 раз — за счёт анализа, стандартизации, параллелизации и устранения лишних действий. И главное: переналадка становится не стихийной, а управляемой.
Что такое SMED — и как он появился в бережливом производстве
SMED (Single Minute Exchange of Die, быстрая переналадка оборудования) — это метод сокращения времени переналадки оборудования до одной цифры в минутах, то есть менее 10. Концепцию быстрой переналадки разработал японский инженер Сигео Синго на производстве Toyota, где задача стояла предельно чётко: обеспечить быстрое переключение между партиями без потери эффективности. До внедрения SMED смена штампов на прессах Toyota могла занимать до 12 часов. Благодаря методике SMED это время было сокращено до менее чем 10 минут, что стало значительным достижением в области быстрой переналадки.
Классическая наладка сегодня может занимать 60, 90, 120 минут и больше — особенно если оборудование старое или под каждый заказ требуется своя оснастка. SMED предлагает структурированный подход, который позволяет системно сократить это время без замены оборудования и капитальных вложений.
Важно понимать: "Single-Minute" — это не жёсткая цель, а символ подхода.
SMED не означает, что наладка обязательно должна длиться меньше 10 минут. Суть в том, чтобы максимально сократить время, сделав процесс:
- стандартизированным,
- визуальным,
- легко обучаемым,
- частично выполняемым до остановки оборудования
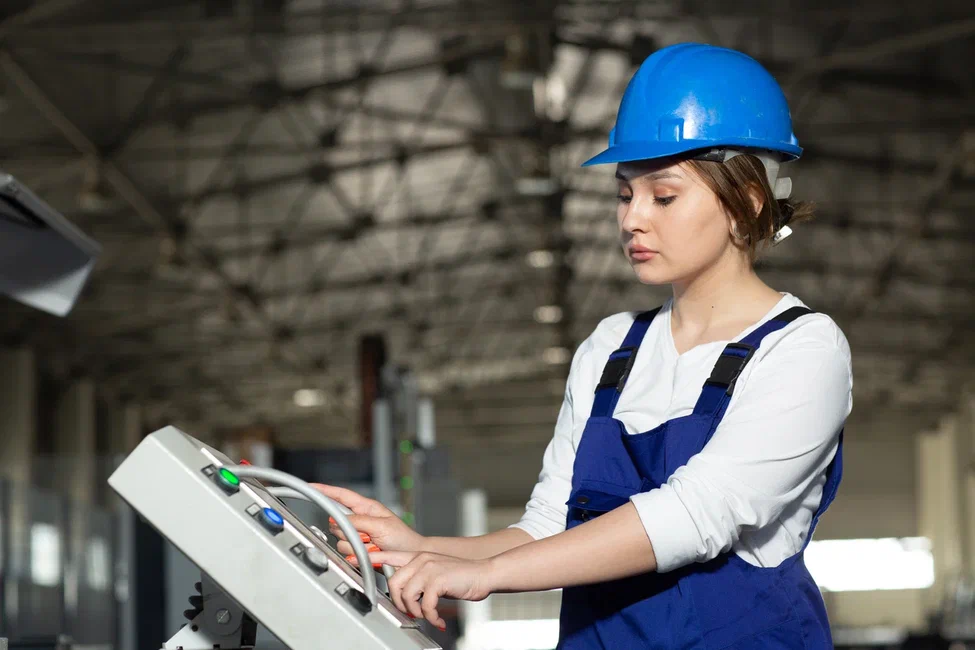
Этапы внедрения SMED: как проходит трансформация процесса
Метод SMED — это не просто "сократить время", а пошаговая перестройка подхода к переналадке. И главная ценность здесь — не в скорости ради скорости, а в устойчивости и предсказуемости. Чтобы внедрение было результативным, важно не перескакивать через этапы.
1. Наблюдение за текущей переналадкой: увидеть, что происходит на самом деле
Первый шаг — это фиксировать реальный процесс переналадки. Не по инструкции и не по памяти сотрудников, а как он есть на самом деле:
Что фиксируем:
- время начала/окончания каждого действия;
- подготовку инструмента;
- перемещения сотрудников;
- ожидание людей, информации, помощи;
- поиски (ключей, насадок, инструкций);
- ошибки, возвраты к предыдущим шагам.
Лучше всего записывать процесс на видео и проводить замеры времени всех действий. Часто уже на этом этапе выявляется, что половину времени занимает не сама наладка, а "поиск ключа", "ожидание бригадира" или "не подготовили оснастку заранее".
Пример: На упаковочной линии завода молочной продукции наладка машины занимала 40 минут. После видеонаблюдения выяснилось, что 15 минут уходит на то, чтобы найти нужную насадку, которая хранилась в другом цехе.
Причина — не «ленивый персонал», а отсутствие стандарта хранения и маркировки. После изменения хранения и закрепления инструмента за рабочим местом этот шаг сократился до 1 минуты — без инвестиций.
2. Разделение всех операций на внутренние и внешние
На этом этапе весь процесс делится на два типа действий:
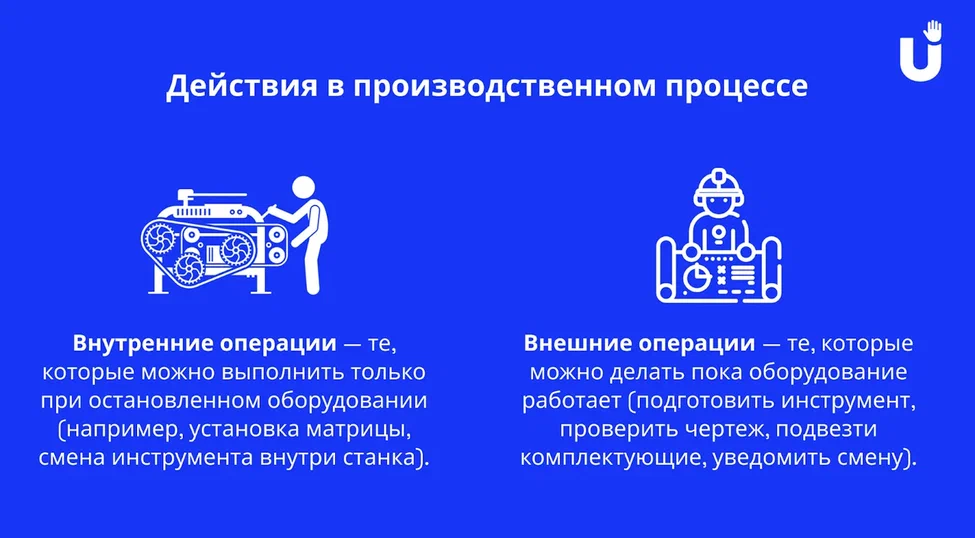
Цель — перевести как можно больше операций из внутренних во внешние, то есть заранее подготовить всё необходимое. Это основной источник сокращения времени.
Пример: На линии розлива напитков переход с одной бутылки на другую включал проверку новых этикеток уже после остановки линии. После внедрения SMED этикетки начали готовить заранее, пока шёл предыдущий цикл, и выиграли 6 минут.
В результате:
- подготовка — параллельно с основной работой,
- остановка сократилась на те же 6 минут,
- никаких инвестиций — только изменение последовательности действий.
Как правило, именно этот этап даёт 30–50% сокращения времени — без модернизации оборудования, только за счёт здравого смысла, наблюдения и переноса операций.
3. Упрощение и стандартизация операций
На этом этапе команда возвращается к каждой операции — особенно внутренней — и задаёт вопрос:
Можно ли сделать это проще, быстрее, без ошибок, одинаково для всех?
Цель: устранить лишние действия (MUDA), сократить вариативность и сделать каждую операцию повторяемой, обучаемой и устойчивой к сбоям.
Устранение лишнего:
- удаление ненужных шагов, повторов, перекладываний
- отказ от «поисков», «согласований», «ожидания»
Стандартизация порядка:
- фиксированная последовательность действий
- чек-листы, цветовые метки, инструкции на оборудовании
Использование универсальных и быстросъёмных элементов:
- магнитные крепления, эксцентрики, быстросменные зажимы
- шаблоны позиционирования, калиброванные элементы
Организация рабочего места (5S):
- инструмент на тени, всё под рукой
- маркировка оснастки и крепежа по размерам и позициям
Пример: На мебельном производстве переналадка станка занимала 35 минут. После внедрения маркировки на всех элементах и перехода на магнитные крепления вместо винтов — сократилась до 11 минут без вложений в технику.
Этот этап часто даёт вторую волну сокращения времени, уже после разделения операций. И именно здесь формируется база для тиражирования SMED на другие линии.
4. Проверка и отработка нового стандарта
После всех изменений процесс снова фиксируется: запускается несколько наладок по новому стандарту, замеряется время, выявляются недочёты. Возможно, часть операций нужно переписать, что-то объяснить рабочим, обучить новичков.
По результатам — корректируются чек-листы, добавляются визуальные элементы, убираются слабые места.
Здесь также формируется визуальный стандарт — инструкция, чек-лист, схема расположения инструментов. Всё должно быть наглядно, чтобы каждый сотрудник мог повторить процесс без "спрашивания у старшего".
5. Постоянное улучшение
SMED — не разовая акция. Даже если удалось сократить время переналадки с 60 до 20 минут, это не предел. Новое оборудование, перестройка логистики, смена персонала — всё влияет на эффективность. Поэтому процесс нужно регулярно пересматривать, отслеживать метрики и искать микроскопические резервы.
Почему нужен пересмотр:
- Появляется новое оборудование или формат продукции
- Меняются операторы (новичкам может сложнее следовать стандарту)
- Перестраивается логистика или график производства
- Изнашивается оснастка, появляются новые задержки
Итог: SMED — это метод, основанный на логике и наблюдательности. Он работает даже в условиях ограниченного бюджета, если правильно организовать подход. А начав с одной пилотной зоны, можно со временем масштабировать принципы на всё производство.
Где SMED работает лучше всего
Методика особенно эффективна там, где часто меняется продукт: малосерийное производство, пищевая промышленность, упаковка, текстиль, печать. Например:

SMED позволяет сэкономить время без покупки нового оборудования. Он работает и на современных цифровых линиях, и на старых станках при правильной организации. Порой достаточно упорядочить инструменты и визуализировать стандарт переналадки — и команда начинает работать быстрее, без лишней суеты.
Что даёт SMED: измеримый эффект
Снижение времени переналадки — основной и очевидный результат. На практике оно сокращается на 30–70% уже в первые месяцы.
Но эффект не ограничивается секундомером. SMED влияет на ключевые аспекты операционной эффективности:
Производственные результаты:
- Рост полезного времени работы оборудования (OEE ↑ на 10–25%)
- Увеличение выпуска продукции без расширения смен
- Быстрее запускаются новые заказы → выше гибкость
- Сокращение WIP (незавершёнки) — не нужно «гнать впрок»
Экономические эффекты:
- Уменьшение затрат на оборудование — нет нужды в дополнительной линии
- Снижение себестоимости за счёт роста загрузки станков
- Меньше запасов = меньше замороженных денег
Организационные плюсы:
- Снижение стресса у наладчиков и операторов — работа по понятной, предсказуемой схеме
- Сокращение зависимости от «ключевых людей» — стандарт воспроизводим
- Рост вовлечённости персонала — люди видят результат своих улучшений
Если переналадка сократилась с 40 до 8 минут — это +32 минуты доступного времени на каждую смену. При 4 переналадках в день — более 2 часов «нового» времени. Это либо +10–15% к выпуску, либо возможность производить меньшими партиями — без затрат.
Заключение: SMED — путь к устойчивому производству
Сегодня производство требует гибкости. Быстрая смена форматов, кастомизация, срочные заказы — всё это требует способности «перестроиться» быстро, без потерь.
SMED даёт такую возможность: он делает переналадку не стрессом, а управляемым процессом. Метод не требует миллионов вложений — только внимание, команда и правильная методика.
Как мы можем помочь
Если вы хотите внедрить SMED, но не знаете, с чего начать, команда Ruqi готова помочь:
- провести аудит текущих переналадок и выделить скрытые потери;
- настроить этапы SMED-подхода на пилотном участке;
- обучить операторов, мастеров и наладчиков стандартам быстрой и безопасной переналадки;
- адаптировать персонал к новым требованиям (включая разработку чек-листов, визуализацию, стандарты рабочего места).
Результат — это не просто «быстрее», а «предсказуемо, воспроизводимо и без стресса». Напишите нам — обсудим задачу и предложим реалистичный план внедрения.