Автомобильное производство – это сложный процесс, где каждая секунда на счету. Эффективность работы во многом зависит от правильной организации пространства, чёткого распределения инструментов и строгого соблюдения стандартов. Именно для этого была разработана система 5S – методология бережливого производства, направленная на создание упорядоченной, чистой и безопасной рабочей среды.
Этот подход помогает не только повысить производительность, но и снизить количество ошибок, минимизировать потери времени и улучшить условия труда. В этой статье разберёмся, как внедряется 5S в автомобильной промышленности, и какие преимущества она даёт предприятиям.
Что такое система 5S?
Методология 5S основана на пяти ключевых принципах, которые помогают структурировать рабочее пространство: сортировка, соблюдение порядка, содержание в чистоте, стандартизация, совершенствование. Данный подход появился в Японии и быстро распространился по всему миру, поэтому оригинальные названия принципов пришли из страны восходящего солнца:
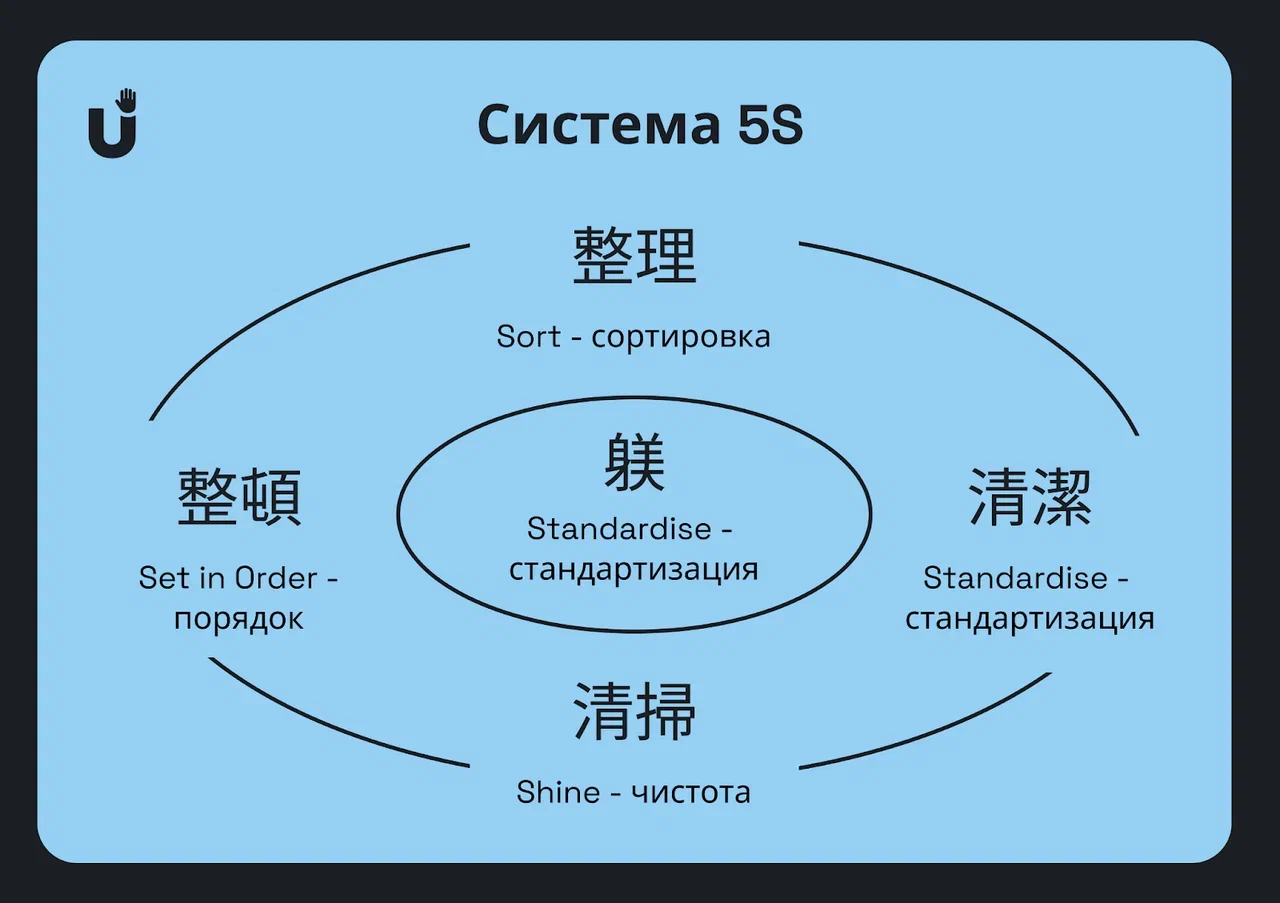
На первый взгляд, 5S кажется простой системой, но на самом деле это мощный инструмент, формирующий культуру бережливого производства. Его цель – не только создать удобное рабочее пространство, но и внедрить дисциплину и системный подход к организации труда.
Как внедряется 5S на автомобильных заводах?
Внедрение 5S проходит в несколько этапов, каждый из которых играет ключевую роль в организации работы.
1. Сортировка (Seiri – Sort)
Персонал анализирует, какие предметы и инструменты действительно нужны на рабочем месте, а какие только занимают пространство.
Как это работает:
- Устраняются ненужные вещи, которые не используются в производственном процессе.
- Всё оборудование и инструменты делятся на категории, зависящие от частоты использования, на основе этого принимаются решения об их расположении в рабочем пространстве.
Пример:
На сборочном участке автозавода сотрудники убирают со станций лишние предметы, оставляя только необходимые инструменты и детали. Это позволяет ускорить процесс сборки и уменьшить время на поиск нужных элементов.
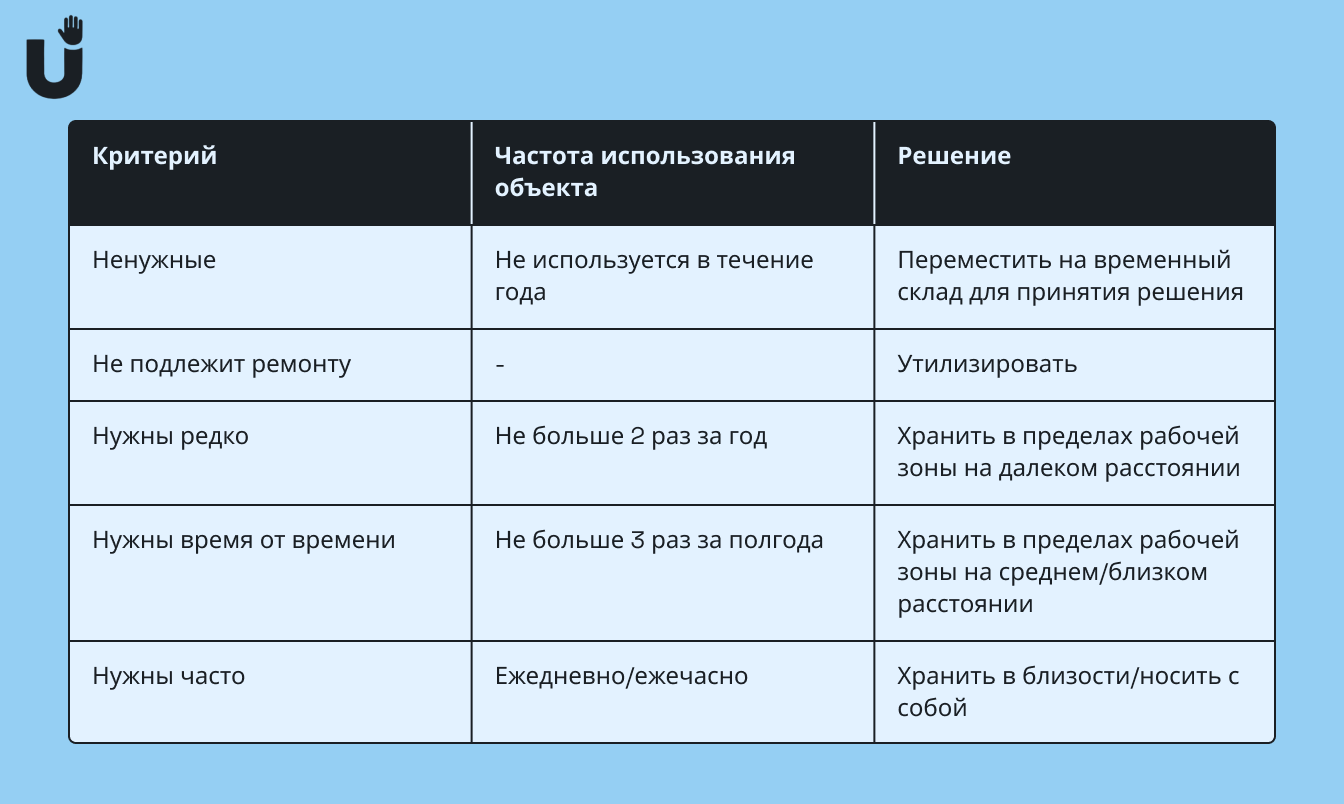
2. Соблюдение порядка (Seiton – Set in Order)
Этот этап направлен на рациональное размещение предметов для удобства работы. Всё должно иметь своё место, чтобы исключить потерю времени на поиски.
Что делается:
- Инструменты располагаются по принципу удобства и безопасности.
- Рабочие зоны маркируются и подписываются.
- Визуализация: создаются стенды, цветовые метки, таблички, схемы расположения оборудования.
Пример:
На заводе по сборке автомобилей механические ключи, гайковёрты и запчасти раскладываются в специализированных держателях рядом с конвейером, а зоны работы маркируются цветными линиями.
3. Содержание в чистоте (Seiso – Shine)
Чистота – это не только порядок, но и контроль состояния оборудования.
Какие меры принимаются:
- Производственные помещения и оборудование регулярно очищаются от грязи, масла, стружки и других загрязнений.
- Проводятся осмотры на наличие повреждений и утечек.
- Работники сами поддерживают чистоту своих рабочих мест.
Пример:
На линиях окраски автомобилей ежедневно убираются остатки краски, а фильтры проверяются и заменяются по регламенту, что снижает вероятность появления дефектов в покрытии.
4. Стандартизация (Seiketsu – Standardise)
После успешного внедрения первых трёх шагов важно закрепить полученные результаты.
Что включает этот этап:
- Разработка стандартных инструкций для сотрудников.
- Введение регламентов по проверке чистоты и порядка.
- Размещение чек-листов и памяток на рабочих местах.
Пример:
На автомобильном заводе каждый сотрудник перед началом смены проходит чек-лист по проверке состояния оборудования, чистоты рабочего места и наличия необходимых инструментов.
5. Совершенствование (Shitsuke – Sustain)
Этот этап самый сложный, так как требует поддержания достигнутых изменений на постоянной основе.
Как это реализуется:
- Регулярное проведение аудитов 5S.
- Внедрение системы предложений от сотрудников по улучшению организации труда.
- Поддержка дисциплины: обучение, наставничество, мотивационные программы.
Пример:
На предприятии Toyota действует практика еженедельных встреч, где сотрудники обсуждают, какие аспекты 5S можно улучшить, и вносят свои предложения по повышению эффективности производства.
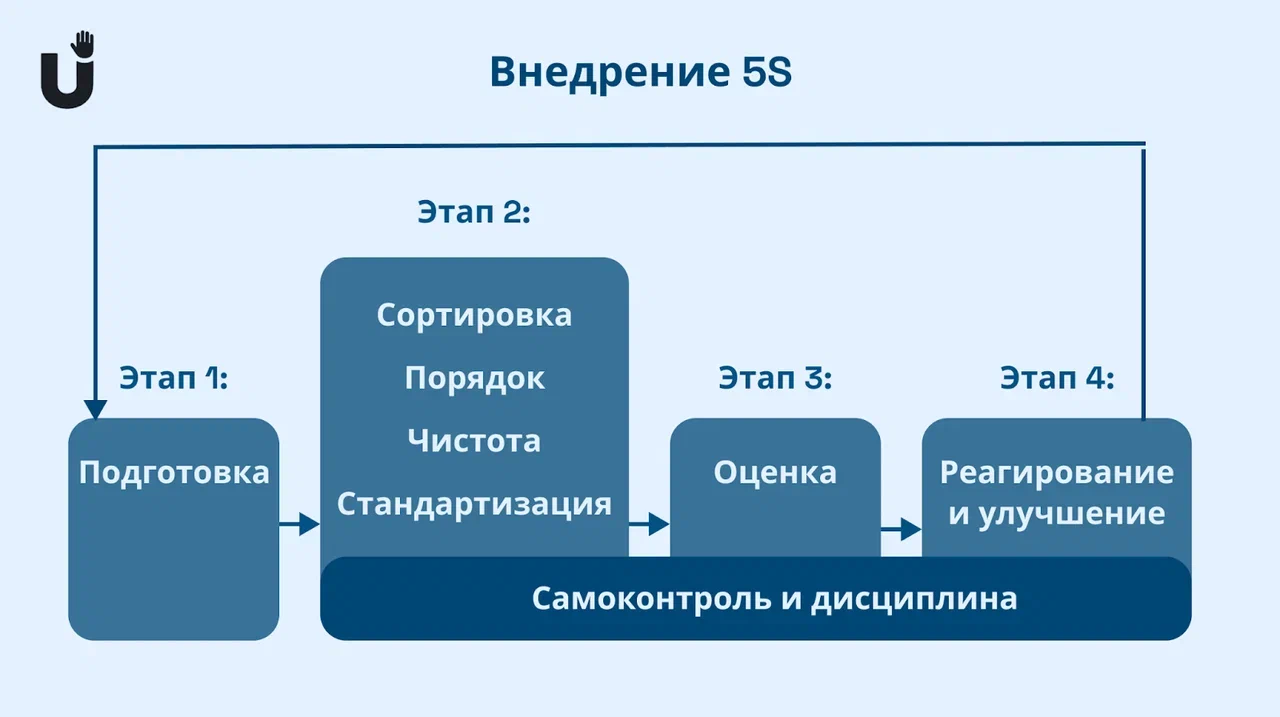
Какие преимущества даёт внедрение 5S?
Ускорение рабочих процессов – поиск инструментов и запчастей занимает меньше времени, производство становится более плавным.
Повышение качества продукции – чистое и организованное рабочее место снижает вероятность брака.
Снижение затрат – минимизируются потери, связанные с дефектами, неэффективным использованием пространства и времени.
Безопасность сотрудников – упорядоченное рабочее место снижает вероятность травм и несчастных случаев.
Повышение дисциплины и мотивации персонала – работники привыкают к порядку и бережному отношению к оборудованию и инструментам.
Практические рекомендации по внедрению 5S
- Обучение и вовлечение персонала – без поддержки сотрудников система 5S не будет работать.
- Применение визуального менеджмента – используйте схемы, метки и таблички для упрощения навигации.
- Регулярные проверки и аудит – внедряйте систему контроля для поддержания порядка.
- Поощрение инициативы сотрудников – создавайте программы мотивации за улучшения.
Заключение
Система 5S – это не просто набор правил, а мощный инструмент оптимизации работы. Внедрение этого метода в автомобильной промышленности помогает предприятиям снизить потери, ускорить производство и повысить качество продукции.
Компании, которые успешно применяют 5S, получают не только чистые и упорядоченные рабочие зоны, но и дисциплинированных, мотивированных сотрудников, которые понимают ценность порядка и эффективности.
Хотите внедрить 5S и повысить качество производства? Мы поможем!
Оптимизация процессов невозможна без квалифицированного персонала и надежного контроля качества. Ruqi предоставляет экспертов в области качества и линейных сотрудников, готовых к работе на вашем предприятии.
Что мы предлагаем?
Решения по управлению качеством – Мероприятия по развитию качества (APQP, PPAP, FMEA, и др.),Анализ проблем, разработка планов и оптимизация затрат на качество, инженерная поддержка
Подбор и управление персоналом – мы обеспечим операторов линий, упаковщиков и инспекторов качества.
Гибкость и эффективность – быстрый подбор кадров, адаптация к пиковым нагрузкам и снижение текучести.
С Ruqi вы получаете не просто работников, а отлаженную систему управления качеством и эффективностью. Оставьте заявку – и мы подберем команду, которая выведет ваше производство на новый уровень!